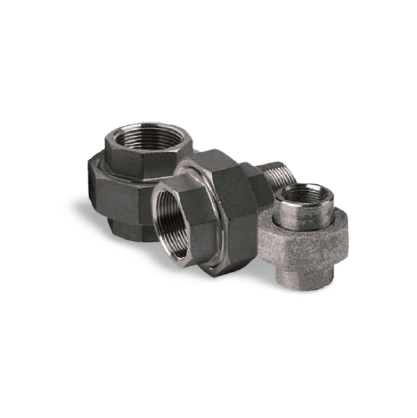
Threaded Union
‘Teshi Fittings’ Threaded Unions: meticulously engineered for a diverse array of industries, including Petroleum, Chemical, Hydraulic, Food, and beyond. Our Threaded Unions exemplify precision craftsmanship and adhere to rigorous international quality standards, ensuring reliable sealing and effortless integration within piping systems. Committed to excellence and exceeding customer expectations, Teshi Fittings delivers superior performance and durability in every fitting. Count on our expertise to provide bespoke solutions for your unique project demands, and encounter the unparalleled quality of Teshi Fittings’ Threaded Unions for all your piping requirements.
Standard Specification of Threaded Union
Threaded Union Dimensions | ASME 16.11, MSS SP-79, MSS SP-95, 83, 95, 97, BS 3799 |
Threaded Union Size | 1/8″ NB TO 4″ NB |
Threaded Union Type | Threaded (S/W) & SCREWED (SCRD) – NPT, BSP, BSPT |
DIN | DIN2605, DIN2615, DIN2616, DIN2617, DIN28011 |
EN | EN10253-1, EN10253-2 |
Threaded Union Production Grades | Stainless Steel, Alloy Steel, Duplex, Nickel Alloys, Low temperature Steel, Carbon Steel, Cupro Nickel |
Threaded Union Form | Threaded Union, Threaded Pipe Union |
Material & Grades of Threaded Union
Stainless Steel Threaded Union | ASTM A182 F304, F304L, F306, F316L, F304H, F309S, F309H, F310S, F310H, F316TI, F316H, F316LN, F317, F317L, F321, F321H, F11, F22, F91, F347, F347H, F904L, ASTM A312/A403 TP304, TP304L, TP316, TP316L. |
Duplex & Super Duplex Steel Threaded Union | ASTM A 182 – F 51, F53, F55 S 31803, S 32205, S 32550, S 32750, S 32760, S 32950. |
Carbon Steel Threaded Union | ASTM/ ASME A 105, ASTM/ ASME A 350 LF 2, ASTM / ASME A 53 GR. A & B, ASTM A 106 GR. A, B & C. API 5L GR. B, API 5L X 42, X 46, X 52, X 60, X 65 & X 70. ASTM / ASME A 691 GR A, B & C |
Nickel Alloy Threaded Union | ASTM / ASME SB 336, ASTM / ASME SB 564 / 160 / 163 / 472, UNS 2200 (NICKEL 200) , UNS 2201 (NICKEL 201 ) , UNS 4400 (MONEL 400 ) , UNS 8020 ( ALLOY 20 / 20 CB 3 ) , UNS 8825 INCONEL (825) , UNS 6600 (INCONEL 600 ) , UNS 6601 (INCONEL 601) , UNS 6625 (INCONEL 625) , UNS 10276 (HASTELLOY C 276) |
Alloy Steel Threaded Union | ASTM / ASME A 182, ASTM / ASME A 335, ASTM / ASME A 234 GR P 1, P 5, P 9, P 11, P 12, P 22, P 23, P 91, ASTM / ASME A 691 GR 1 CR, 1 1/4 CR, 2 1/4 CR, 5 CR, 9CR, 91 |
Copper Alloy Steel Threaded Union | ASTM / ASME SB 111 UNS NO. C 10100 , C 10200 , C 10300 , C 10800 , C 12000, C 12200, C 70600 C 71500, ASTM / ASME SB 466 UNS NO. C 70600 ( CU -NI- 90/10) , C 71500 ( CU -NI- 70/30) |
Dimension of Threaded Union
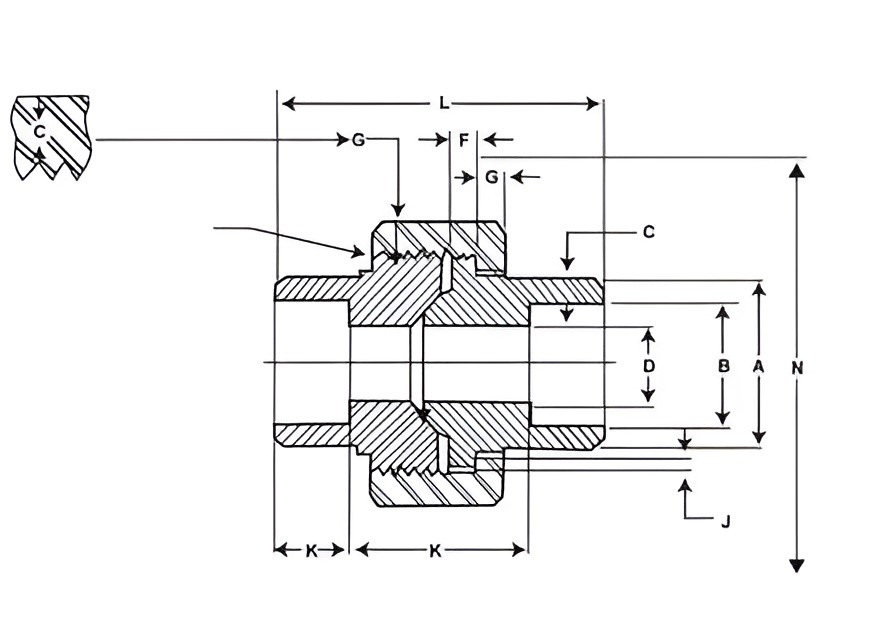
DIMENSIONS OF THREADED UNION (BS3799) (in mm) | ||||||||||||
Nom. Pipe Size | Pipe End Min | Socket Bore Dia. | Socket Wall Min. | Water Way Bore | Laying Length | Male Flange Min. | Nut Min. | Threads Per 25.4 Max | Bearing Min. | Depth of Socket Min. | Length Assem. Nominal | Clear Assem. Nut |
A | B | C | D | E | F | G | H | J | K | L | N | |
1/8 | 21.8 | 10.92 10.67 | 3.17 | 6.83 6.43 | 22.4 19.0 | 3.17 | 3.17 | 16 | 1.24 | 9.6 | 41.1 | 49.0 |
¼ | 21.8 | 14.22 13.97 | 3.30 | 9.85 9.45 | 22.4 19.0 | 3.17 | 3.17 | 19 | 1.24 | 9.6 | 41.4 | 49.0 |
3/8 | 25.9 | 17.78 17.53 | 3.48 | 13.92 13.51 | 26.9 20.6 | 3.43 | 3.43 | 14 | 1.37 | 9.6 | 46.0 | 55.0 |
½ | 31.2 | 21.84 21.59 | 4.06 | 17.47 17.07 | 26.9 20.6 | 3.68 | 3.68 | 14 | 1.50 | 9.6 | 49.0 | 57.0 |
¾ | 37.1 | 27.18 26.92 | 4.27 | 21.79 21.39 | 31.8 25.4 | 4.06 | 4.06 | 11 | 1.68 | 12.7 | 56.9 | 67.0 |
1 | 45.5 | 34.04 33.78 | 4.95 | 28.14 27.74 | 34.3 26.2 | 4.57 | 4.44 | 11 | 1.85 | 12.7 | 62.0 | 79.0 |
11/4 | 54.9 | 42.67 42.42 | 5.28 | 35.76 35.36 | 40.6 32.5 | 5.33 | 5.21 | 11 | 2.13 | 12.7 | 71.1 | 94.0 |
11/2 | 61.5 | 48.77 48.51 | 5.54 | 41.61 41.20 | 42.2 34.0 | 5.84 | 5.59 | 10 | 2.31 | 12.7 | 75.5 | 111.0 |
2 | 75.2 | 61.47 61.21 | 6.05 | 52.53 52.12 | 45.3 37.3 | 6.60 | 6.35 | 10 | 2.69 | 15.8 | 86.1 | 132.0 |
21/2 | 91.7 | 74.17 73.66 | 7.65 | 64.72 64.31 | 61.7 52.1 | 7.49 | 7.11 | 8 | 3.07 | 15.8 | 102.4 | 148.0 |
3 | 109.2 | 90.17 89.66 | 8.31 | 77.67 77.27 | 63.8 53.6 | 8.25 | 8.00 | 8 | 3.53 | 15.8 | 109.0 | 175.0 |
Manufacturing process and features of Threaded Union
The manufacturing process of butt weld caps involves several key steps to ensure their structural integrity and suitability for diverse applications. Here’s an overview of the process and the distinctive features of butt weld caps:
Manufacturing Process:
- Material Selection : Choice of Materials Select appropriate materials such as stainless steel, carbon steel, brass, or plastic, depending on the application requirements and environmental conditions.
- Forming : Initial Shaping Use forging, casting, or machining to create the basic shape of the union. The union typically consists of two or more separate components: the body, the nuts, and sometimes a middle ring.
- Thread Cutting : Internal and External Threads Cut internal and external threads on the union parts using precision machinery to ensure a tight, leak-proof connection. The threads are usually standardized, such as NPT (National Pipe Thread) or BSP (British Standard Pipe).
- Assembly : Component Assembly Assemble the union components, which may include the body, nuts, and middle ring. The parts are screwed together to form a complete union. In some designs, additional sealing elements like gaskets may be included.
- Surface Treatment : Finishing Apply surface treatments such as coating, polishing, or plating to enhance corrosion resistance and improve appearance. Treatments may include galvanizing, anodizing, or passivation.
- Quality Control : Testing Conduct various tests to ensure the union meets industry standards and specifications. Tests may include pressure testing, thread inspection, and dimensional checks.
Features of Threaded Union :
- Threaded Connections : Easy Assembly and Disassembly Threaded unions allow for quick and convenient connections and disconnections without requiring special tools.
- Leak-Proof Seal : Reliable Performance The threaded design ensures a tight seal that prevents leaks, making the union suitable for various fluid and gas applications.
- Versatility : Wide Range of Applications Used in plumbing, HVAC, chemical processing, oil and gas, and other industries for connecting pipes or components of different sizes and materials.
- Durable Construction : Robust Design Constructed from high-quality materials to withstand pressure, temperature, and corrosion, ensuring long-term performance.
- Standardization : Compliance with Standards Threaded unions are manufactured to meet various industry standards, such as ANSI, ISO, or ASTM, ensuring compatibility and reliability.
- Ease of Maintenance : Convenient Repairs The ability to easily disassemble and reassemble threaded unions facilitates maintenance and repair of piping systems.
- Variety of Sizes and Types : Customizable Solutions Available in various sizes, pressure ratings, and materials to suit different applications and requirements.
Threaded unions are essential components in piping systems, offering easy assembly, a reliable seal, and durability. The manufacturing process involves selecting materials, forming, threading, assembling, and surface treatment, followed by rigorous quality control. Their features make them suitable for a wide range of applications across different industries.
Application Of Threaded Union
Oil and Gas | Facilitate maintenance and modifications in pipelines and distribution systems. |
Plumbing Systems | Used for easy disassembly in residential, commercial, and industrial plumbing. |
Water Supply Networks | Facilitate quick maintenance and modifications in water distribution systems. |
HVAC Systems | Enable easy access for maintenance in heating and cooling installations. |
Process Industries | Used for quick disassembly in chemical, pharmaceutical, and food processing pipelines. |
Fire Protection Systems | Essential for quick installation and maintenance of fire sprinkler components. |
Industrial Equipment | Connect fluid lines in machinery for ease of installation and maintenance. |
Shipbuilding and Marine | Used onboard ships and offshore platforms for connecting piping systems. |
General Plumbing and Mechanical | Found in various applications where easy assembly and disassembly are needed. |
Agricultural Irrigation | Connect irrigation pipes and valves for maintenance and adjustments. |
Threaded Union Available Types
Forged Steel Unions | MS Forged Union |
Threaded Union Coupling | 3000# Npt Threaded Union |
Threaded Copper Union | Threaded Pipe Union Fittings |
Galvanized Threaded Union | Threaded Orifice Union |
9000# Threaded Pipe Union | Threaded Reducing Union |
Male Threaded Socket Union | Socket Weld X Threaded Union |
Male X Female Threaded Union | Screwed Union Pipe Fittings |
Carbon Steel Threaded Union | High Pressure Threaded Union |
ASTM A182 SS Threaded Union | Duplex Steel Threaded Union |
Titanium Forged Threaded Unions | Inconel Forged Threaded Unions |
Super Duplex Steel Threaded Union | Copper Nickel Threaded Union |
6000# Threaded Union Fitting | BS 3799 Threaded Union Female Male |
High Nickel Alloy Forged Steel Union | Hastelloy Screwed Union Pipe Fittings |
Forged Threaded Adapter Union Fitting | Stainless Steel Threaded Union |
Others Products
Frequently Asked Questions
Most frequent questions and answers