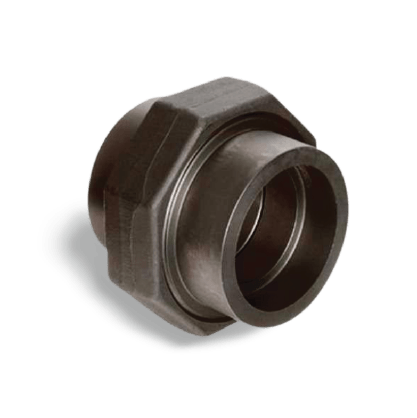
Socket Weld Union
‘Teshi Fittings’ premier Socket Weld Unions, meticulously crafted for various industries including Petroleum, Chemical, Hydraulic, Food, and more. Engineered with precision and manufactured to meet stringent international quality standards, our Socket Weld Unions ensure dependable sealing and seamless integration within piping systems. Committed to excellence and exceeding customer expectations, Teshi Fittings guarantees superior performance and longevity in every fitting, offering tailored solutions to meet specific project requirements. Trust in Teshi Fittings’ expertise for all your piping needs and experience the unmatched quality of our Socket Weld Unions.
Standard Specification of Socket Weld Union
Dimensions | ASME 16.11, MSS SP-79, MSS SP-95, 83, 95, 97, BS 3799 |
Size | 1/2″NB TO 4″NB IN |
Type | Socket Weld (S/W) & SCREWED (SCRD) – NPT, BSP, BSPT |
DIN | DIN2605, DIN2615, DIN2616, DIN2617, DIN28011 |
EN | EN10253-1, EN10253-2 |
Schedule | SCH20, SCH30, SCH40, STD, SCH80, XS, SCH60, SCH80, SCH120, SCH140, SCH160, XXS |
Form | Socket Weld Union, Socket Weld Pipe Union, Socket Weld Orifice Union, Forged Union, Socket Weld Union Fittings |
Material & Grades of Socket Weld Union
Stainless Steel Socket Weld Union | ASTM A182 F304, F304L, F306, F316L, F304H, F309S, F309H, F310S, F310H, F316TI, F316H, F316LN, F317, F317L, F321, F321H, F11, F22, F91, F347, F347H, F454L, ASTM A312/A403 TP304, TP304L, TP316, TP316L |
Duplex & Super Duplex Steel Socket Weld Union | ASTM A 182 – F 51, F53, F55 S 31803, S 32205, S 32550, S 32750, S 32760, S 32950. |
Carbon Steel Socket Weld Union | ASTM A105, A350 LF2, A106 Gr.B, A234 WPB |
Low Temperature Carbon Steel Socket Weld Union | ASTM/ASME A420 SA/420 WPL3, WPL6 |
Alloy Steel Socket Weld Union | ASTM / ASME A182, ASTM / ASME A335 GR P 1, P 5, P 9, P 11, P 12, P 22, P 23, P 91, ASTM / ASME A691 GR 1 CR, 1 1/4 CR, 2 1/4 CR, 5 CR, 9CR, 91 |
Nickel Alloy Socket Weld Union | ASTM B336, ASME SB336, Nickel 200 (UNS No. No2200), Nickel 201 (UNS No. N02201), Monel 400 (UNS No. N04400), Monel 500 (UNS No. N05500), Inconel 800 (UNS No. N08800), Inconel 825 (UNS No. N08825), Inconel 600 (UNS No. N06600), Inconel 625 (UNS No. N06625), Inconel 601 (UNS No. N06601), Hastelloy C 276 (UNS No. N10276), Alloy 20 (UNS No. N08020), Titanium (Grade I & II), Copper Nickel (Cupro-Nickel 90/10 & 70/30). |
Dimension of Socket Weld Union

ANSI/ASME B16.11 SOCKET WELD UNION DIMENSIONS
Nominal Diameter | Outside Diameter | Wall Thickness | Socket Bore | Water way Bore | Depth of Socket | Length Assem Nominal | |||
Dmin | Cmin | d1 | d2 | Jmin | L | ||||
DN | NPS | Socket | Threaded | Socket | Threaded | Socket | Socket & Threaded | Socket | Socket & Threaded |
6 | 1/8 | 21.8 | 14.7 | 3.2 | 2.5 | 10.65 | 6.43 | 10 | 41.4 |
8 | 1/4 | 21.8 | 19.0 | 3.3 | 3.1 | 14.10 | 9.45 | 10 | 41.4 |
10 | 3/8 | 25.9 | 22.9 | 3.5 | 3.2 | 17.55 | 13.51 | 10 | 46.0 |
15 | 1/2 | 31.2 | 27.7 | 4.1 | 3.8 | 21.70 | 17.07 | 10 | 49.0 |
20 | 3/4 | 37.1 | 33.5 | 4.3 | 4.0 | 27.05 | 21.39 | 13 | 56.9 |
25 | 1 | 45.5 | 41.4 | 5.0 | 4.6 | 33.80 | 27.74 | 13 | 62.0 |
32 | 11/4 | 54.9 | 50.5 | 5.3 | 4.9 | 42.55 | 35.36 | 13 | 71.1 |
40 | 11/2 | 61.5 | 57.2 | 5.6 | 5.1 | 48.65 | 41.20 | 13 | 76.5 |
50 | 2 | 75.2 | 70.1 | 6.1 | 5.6 | 61.10 | 52.12 | 16 | 86.1 |
65 | 21/2 | 91.7 | 85.3 | 7.7 | 7.1 | 73.80 | 64.31 | 16 | 102.4 |
80 | 3 | 109.2 | 102.4 | 8.4 | 7.7 | 89.80 | 77.27 | 16 | 109.0 |
CLASS 3000 Socket Weld Union | ||||||||||||
PIPE SIZE | 1/8 | 1/4 | 3/8 | 1/2 | 3/4 | 1 | 1-1/4 | 1-1/2 | 2 | 2-1/2 | 3 | 4 |
A | 1.375 | 1.375 | 1.625 | 1.813 | 2.250 | 2.562 | 3.063 | 3.438 | 4.063 | 4.875 | 5.688 | 6.875 |
B | 1.688 | 1.688 | 1.813 | 1.938 | 2.250 | 2.438 | 2.813 | 3.000 | 3.375 | 4.031 | 4.313 | 8.000 |
C | 0.865 | 0.865 | 1.025 | 1.235 | 1.465 | 1.795 | 2.165 | 2.425 | 2.965 | 3.615 | 4.305 | 5.415 |
D | 0.426 | 0.560 | 0.693 | 0.859 | 1.071 | 1.335 | 1.682 | 1.922 | 2.410 | 2.910 | 3.536 | 4.545 |
E | 0.813 | 0.813 | 0.938 | 0.938 | 1.125 | 1.188 | 1.438 | 1.500 | 1.625 | 2.250 | 2.313 | 5.000 |
LBS | 0.40 | 0.38 | 0.52 | 0.73 | 1.19 | 1.66 | 2.66 | 3.42 | 5.36 | 9.12 | 12.58 | 17.50 |
CLASS 6000 Socket Weld Union | ||||||||||||
PIPE SIZE | 1/8 | 1/4 | 3/8 | 1/2 | 3/4 | 1 | 1-1/4 | 1-1/2 | 2 | 2-1/2 | 3 | 4 |
A | 1.375 | 1.625 | 1.813 | 2.250 | 2.562 | 3.063 | 3.438 | 4.063 | 4.875 | 5.688 | 6.875 | — |
B | 1.688 | 1.813 | 1.938 | 2.250 | 2.438 | 2.813 | 3.000 | 3.375 | 4.031 | 4.313 | 8.000 | — |
C | 0.865 | 1.025 | 1.235 | 1.465 | 1.795 | 2.165 | 2.425 | 2.965 | 3.615 | 4.305 | 5.415 | — |
D | 0.426 | 0.560 | 0.693 | 0.859 | 1.071 | 1.335 | 1.682 | 1.922 | 2.410 | 2.910 | 3.536 | — |
E | 0.813 | 0.813 | 0.938 | 0.938 | 1.125 | 1.188 | 1.438 | 1.500 | 1.625 | 2.250 | 5.750 | — |
LBS | 0.48 | 0.56 | 0.75 | 1.35 | 2.01 | 3.17 | 3.92 | 6.60 | 10.12 | 14.00 | 40.891 | — |
CLASS 9000 Socket Weld Union | ||||||||||||
PIPE SIZE | 1/8 | 1/4 | 3/8 | 1/2 | 3/4 | 1 | 1-1/4 | 1-1/2 | 2 | 2-1/2 | 3 | 4 |
A | 1.750 | 2.000 | 2.250 | 2.563 | 3.063 | 3.688 | 4.313 | 5.000 | 5.750 | 6.875 | — | — |
B | 2.500 | 2.563 | 2.938 | 3.250 | 3.750 | 4.000 | 4.625 | 4.813 | 5.563 | 6.25 | — | — |
C | 1.000 | 1.250 | 1.500 | 1.750 | 2.250 | 2.500 | 3.000 | 3.625 | 4.250 | 5.000 | — | — |
D | 0.426 | 0.560 | 0.693 | 0.859 | 1.071 | 1.335 | 1.682 | 1.922 | 2.410 | 2.910 | — | — |
E | 1.720 | 1.688 | 1.938 | 2.000 | 2.375 | 2.375 | 3.000 | 2.938 | 3.188 | 3.750 | — | — |
LBS | 0.89 | 1.045 | 1.955 | 3.29 | 5.34 | 7.99 | 12.73 | 18.34 | 26.36 | 37.07 | — | — |
Manufacturing process and features of Socket Weld Union
Socket weld pipe fittings are commonly used in piping systems where high-pressure and high-temperature conditions are expected. Here are the key aspects of their manufacturing process and features:
Manufacturing Process:
- Material Selection: Socket weld unions are typically crafted from forged materials such as carbon steel, stainless steel, or alloy steel. These materials are chosen for their strength and durability in high-pressure environments.
- Forging: The manufacturing begins with forging, where heated billets of selected materials are shaped using forging dies. This process ensures the unions have robust grain structure and mechanical properties required for high-pressure applications.
- Machining: Post-forging, the unions undergo precise machining to meet dimensional specifications like ASME B16.11. This step ensures accurate dimensions and smooth surfaces, critical for reliable performance.
- Heat Treatment: Depending on material requirements, unions may undergo heat treatments like normalization or tempering to enhance mechanical properties such as hardness and toughness.
- Quality Control: Stringent quality control measures are employed throughout manufacturing. This includes dimensional checks, surface finish inspections, and material integrity tests to ensure adherence to standards and consistent quality.
Features of Socket Weld Union:
- Socket Weld Connection: Unions facilitate pipe connections via insertion into a recessed area (socket) and subsequent fillet welding. This method ensures a secure, leak-proof joint.
- High Pressure Capability: Designed for high-pressure applications, socket weld unions typically withstand Class 3000 or 6000 pressures, ensuring reliability under demanding conditions.
- Compact Design: Featuring a space-efficient design compared to butt weld alternatives, unions are suitable for installations where space constraints are a concern.
- Smooth Flow: Their smooth interior minimizes turbulence and pressure drops in fluid flow, beneficial for maintaining efficient operations in high-velocity systems.
- Strength and Reliability: Thanks to forged construction and weld integrity, socket weld unions offer robust strength and reliability, crucial for industries like oil and gas, chemical processing, and power generation.
- Easy Installation and Maintenance: Unions are straightforward to install and dismantle, streamlining maintenance procedures and minimizing downtime compared to fully welded alternatives.
- Versatility: Available in various sizes, configurations (e.g., straight, reducing), and materials, socket weld unions accommodate diverse piping system needs across industries.
Socket weld unions play a pivotal role in industries requiring dependable connections under high pressures and temperatures. Their rigorous manufacturing process ensures they meet exacting standards, making them indispensable for critical applications demanding reliability and performance.
Application Of Socket Weld Union
Oil and Gas Pipeline | Stainless Steel Forged Socket Weld Unions are essential for their durability and resistance to corrosion in pipeline systems. |
Chemical Industry | These unions are used where chemical resistance and leak-proof joints are critical for safety and operational efficiency. |
Plumbing | Alloy Steel Socket Weld Unions are employed in plumbing applications where strength and ease of installation are advantageous. |
Heating | Forged Socket Weld End Unions play a role in heating systems, ensuring secure connections under high temperatures and pressures. |
Water Supply Systems | Socket Weld Forged Unions are utilized to maintain reliable joints in water distribution networks. |
Power Plants | ANSI B16.11 Forged Socket Weld Unions contribute to the efficiency and reliability of piping systems within power generation facilities. |
Paper & Pulp Industry | Socket Weld Unions are used in this industry for their strength and resilience in handling various fluids and chemicals. |
General Purpose Applications | Forged Socket Weld Unions are versatile and find use in a wide range of general industrial applications where robust pipe connections are required. |
Fabrication Industry | These unions are integral in fabrication processes where strong, dependable joints are essential for structural integrity. |
Food Processing Industry | Forged Socket Weld Unions meet stringent hygiene standards and are used in processing and conveying food products safely. |
Structural Pipe | Used in the construction and maintenance of structural pipe systems where reliability and longevity are paramount. |
Socket Weld Union Available Types
Forged Socket weld Union | Socket Weld Union 3000 |
Socket Weld Union Fittings | 2 Socket weld Union |
ASME B16.11 Socket Weld Pipe Union | 3000LB Socket Weld Union |
4 Socket Weld Union | Class 6000 Socket Weld Union |
ANSI B16.11 Forged Socket Weld Union | BS 3799 Forged Socket Weld Union |
Socket Weld Forged Union | Socket Weld Union Weight |
2 Socket Weld Union | High Quality Socket weld Union |
3000# Forged Socket Weld Union | ANSI B16.11 Socket Weld Pipe Union |
Union doble Socket Weld | Socket Weld O-ring Union |
Tube Socket Weld Union | Socket Weld Hammer Union |
Union Universal Socket Weld | Tuerca Union Socket Weld |
3/4 Socket Weld Union | Socket Weld Tube Union |
Union Socket Weld 6000 | Socket Weld Dielectric Union |
1 1/2 Socket Weld Union | Socket Weld Orifice Union |
Others Products
Frequently Asked Questions
Most frequent questions and answers