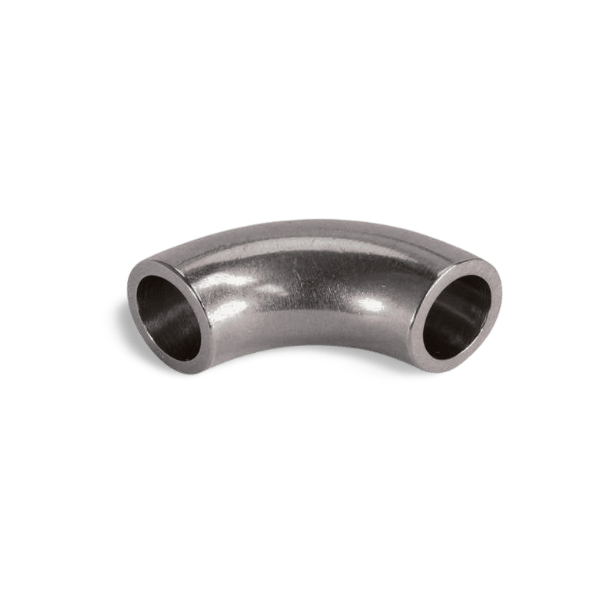
Miter Bend
Teshi Fittings, a premier manufacturer of pipe fittings, offers high-quality Miter Bends designed for various industries including Petroleum, Chemical, Hydraulic, Food, and more. Engineered with meticulous precision and adherence to international quality standards, our Miter Bends provide efficient and reliable solutions for angular direction changes in piping systems. With a commitment to excellence and customer satisfaction, Teshi Fittings delivers superior performance and durability in every fitting, offering tailored solutions to meet specific project requirements. Experience the difference with Teshi Fittings’ Miter Bends and trust in our expertise for all your piping needs.
Standard Specification of Miter Bend
Outside Diameter (OD) | 1/2″NB TO 48″NB IN |
Dimensions | ASME/ANSI B16.9, MSS-SP-43 Type A, MSS-SP-43 Type B, JIS B2312, JIS B2313, ASME B16.28 |
Wall Thickness | SCH5, SCH10, SCH20, SCH30, SCH40, STD, SCH80, XS, SCH60, SCH80, SCH120, SCH140, SCH160, XXS / 3mm – 40mm |
Mitered Bending Radius | Mitered Bending Radius |
Important Grades | ASTM A403 WP 304 / 304L / 304H / 316 / 316L / 317 / 317L / 321 / 310 / 347 / 904L |
Production Materials | Stainless Steel, Alloy Steel, Carbon Steel, Duplex, Nickel Alloys, Cupro Nickel, Low Temperature Steel |
Material & Grades of Miter Bend
Stainless Steel | ASTM /ASME A/SA 213 / 249 / 269 / 312 / 358 CL. I to V – 304 , 304L , 304H, 309S ,309H , 310S, 310H , 316 , 316TI , 316H , 316 LN , 317 , 317L , 321 , 321H , 347 , 347 H , 904L |
Duplex & Super Duplex Steel | ASTM A815, ASME SA815 UNS NO S31803, UNS NO S32205, UNS S32750, UNS S32950. Werkstoff No. 1.4462 |
Carbon Steel | ASTM A234 WPB, WPBW, WPHY 70, WPHY 65, WPHY 60, WPHY 52, WPHY 46, & WPHY 42. |
Nickel Alloy | UNS 10276 (HASTELLOY C 276), UNS 6625 (INCONEL 625), UNS 6601 (INCONEL 601), UNS 6600 (INCONEL 600), UNS 8825 (INCONEL 825), UNS 8020 (ALLOY 20 / 20 CB 3), UNS 4400 (MONEL 400), UNS 2201 (NICKEL 201), ASTM / ASME SB 336 UNS 2200 (NICKEL 200) |
Alloy Steel | ASTM / ASME A/SA 234 Gr. WP1, WP5, WP9, WP11, WP12, WP22, WP91 |
Low Temperature | ASTM A420 WPL6, ASTM A420 WPL3 |
Dimension of Miter Bend
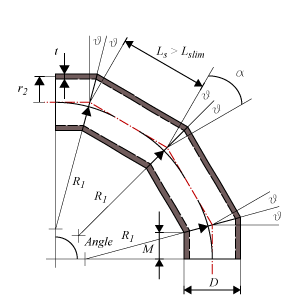
Size in. | CLR Std. | OD in. | ID in. | Weight (lbs.) | Flange | |||||||||
---|---|---|---|---|---|---|---|---|---|---|---|---|---|---|
30° | 45° | 60° | 90° | Hgt. (H) in. | Thk. (T) in. | ID in. | B.C. in. | OD in. | Bolts # | Hole Dia. in. | ||||
3 | 1 | 3.07 | 3.00 | 1.60 | 1.75 | 1.60 | 1.75 | 1.00 | 0.1250 | 3.06 | 4.31 | 5.06 | 6 | 0.281 |
4 | 1 | 3.89 | 3.82 | 2.00 | 2.25 | 2.00 | 2.25 | 1.00 | 0.1250 | 4.06 | 5.31 | 6.06 | 6 | 0.281 |
5 | 1 | 4.91 | 4.84 | 2.75 | 2.80 | 2.75 | 2.80 | 1.00 | 0.1250 | 5.06 | 6.31 | 7.06 | 6 | 0.281 |
6 | 1 | 5.93 | 5.86 | 3.65 | 3.85 | 3.65 | 3.85 | 1.25 | 0.1250 | 6.09 | 7.31 | 8.91 | 6 | 0.281 |
7 | 1 | 6.94 | 6.87 | 4.80 | 4.90 | 4.80 | 4.90 | 1.25 | 0.1250 | 7.13 | 8.50 | 9.63 | 6 | 0.375 |
8 | 1.5 | 7.93 | 7.86 | 6.87 | 7.66 | 6.87 | 7.66 | 1.25 | 0.1250 | 8.13 | 9.56 | 10.63 | 6 | 0.375 |
9 | 1.5 | 8.92 | 8.85 | 9.48 | 8.45 | 9.48 | 8.45 | 1.25 | 0.1250 | 9.13 | 10.63 | 11.63 | 6 | 0.438 |
10 | 1.5 | 9.93 | 9.86 | 12.98 | 15.47 | 12.98 | 15.47 | 1.25 | 0.1250 | 10.13 | 11.81 | 12.63 | 6 | 0.438 |
11 | 1.5 | 10.92 | 10.85 | 15.49 | 17.60 | 15.49 | 17.60 | 1.25 | 0.1250 | 11.13 | 12.75 | 13.63 | 6 | 0.438 |
12 | 1.5 | 11.99 | 11.92 | 18.67 | 19.33 | 18.67 | 19.33 | 1.50 | 0.1250 | 12.13 | 14.00 | 15.13 | 8 | 0.438 |
13 | 1.5 | 13.00 | 12.92 | 21.44 | 22.40 | 21.44 | 22.40 | 1.50 | 0.1250 | 13.13 | 15.00 | 16.13 | 8 | 0.438 |
14 | 1.5 | 13.99 | 13.91 | 24.92 | 25.39 | 24.92 | 25.39 | 1.50 | 0.1250 | 14.13 | 16.00 | 17.13 | 8 | 0.438 |
15 | 1.5 | 14.99 | 14.91 | 27.80 | 27.90 | 27.80 | 27.90 | 1.50 | 0.1250 | 15.13 | 17.00 | 18.13 | 8 | 0.438 |
16 | 1.5 | 16.00 | 15.92 | 30.25 | 30.51 | 30.25 | 30.51 | 1.50 | 0.1875 | 16.13 | 18.00 | 19.13 | 8 | 0.438 |
17 | 1.5 | 17.00 | 16.92 | 33.69 | 32.30 | 33.69 | 32.30 | 1.50 | 0.1875 | 17.13 | 19.00 | 20.13 | 8 | 0.438 |
18 | 1.5 | 17.99 | 17.91 | 36.86 | 34.67 | 36.86 | 34.67 | 1.50 | 0.1875 | 18.13 | 20.00 | 21.13 | 8 | 0.438 |
20 | 1.5 | 20.00 | 19.92 | 40.52 | 41.99 | 40.52 | 41.99 | 1.50 | 0.1875 | 20.13 | 21.75 | 23.13 | 12 | 0.438 |
22 | 1.5 | 22.01 | 21.93 | 45.95 | 46.90 | 45.95 | 46.90 | 1.50 | 0.1875 | 22.13 | 23.75 | 25.13 | 12 | 0.438 |
24 | 1.5 | 23.98 | 23.9 | 58.95 | 70.96 | 58.95 | 70.96 | 1.50 | 0.1875 | 24.13 | 25.88 | 27.13 | 12 | 0.438 |
26 | 1.5 | 26.07 | 25.94 | 75.08 | 89.12 | 75.08 | 89.12 | 2.00 | 0.1875 | 26.13 | 28.38 | 30.13 | 16 | 0.438 |
28 | 1.5 | 28.07 | 27.94 | 82.97 | 99.19 | 82.97 | 99.19 | 2.00 | 0.1875 | 28.13 | 30.38 | 32.13 | 16 | 0.438 |
30 | 1.5 | 30.06 | 29.94 | 91.71 | 110.26 | 91.71 | 110.26 | 2.00 | 0.1875 | 30.13 | 32.38 | 34.13 | 16 | 0.438 |
32 | 1.5 | 32.06 | 31.94 | 100.23 | 121.38 | 100.23 | 1.38 | 2.00 | 0.1875 | 32.13 | 34.38 | 36.13 | 16 | 0.438 |
34 | 1.5 | 33.93 | 33.06 | 132.18 | 133.52 | 132.18 | 133.52 | 2.00 | 0.1875 | 34.13 | 36.38 | 38.13 | 16 | 0.438 |
36 | 1.5 | 36.06 | 35.93 | 122.29 | 149.04 | 122.29 | 149.04 | 2.00 | 0.1875 | 36.13 | 38.38 | 40.13 | 16 | 0.438 |
38 | 1.5 | 38.08 | 37.94 | 132.58 | 162.31 | 132.58 | 162.31 | 2.00 | 0.1875 | 38.13 | 40.38 | 42.13 | 24 | 0.438 |
40 | 1.5 | 40.08 | 39.94 | 142.99 | 176.20 | 142.99 | 176.20 | 2.00 | 0.1875 | 40.13 | 42.38 | 44.13 | 24 | 0.438 |
Manufacturing process and features of Miter Bend
Manufacturing Process:
- Material Selection : Select appropriate materials such as carbon steel, stainless steel, or alloy steel based on application requirements and environmental conditions.
- Cutting : The pipe is cut at specific angles to create the sections that will form the miter bend. The angle of the cut determines the bend’s degree.
- Beveling : The edges of the cut sections are beveled to prepare them for welding. This ensures a strong weld and proper alignment of the sections.
- Alignment : The cut sections are aligned precisely to ensure the correct angle and radius of the bend. Proper alignment is crucial for the bend to function correctly in the piping system.
- Welding : The beveled edges of the sections are welded together using a suitable welding process (e.g., TIG, MIG, or SMAW). Multiple weld passes may be required to achieve a strong and leak-free joint.
- Inspection : The welds and the overall miter bend are inspected for defects such as cracks, porosity, or misalignment. Non-destructive testing methods like radiography or ultrasonic testing may be used.
- Heat Treatment : Depending on the material and application, the miter bend may undergo heat treatment to relieve stresses induced during welding and to enhance mechanical properties.
- Surface Treatment : The miter bend may be subjected to surface treatments such as sandblasting, painting, or coating to improve corrosion resistance and surface finish.
- Final Inspection : A final inspection is performed to ensure that the miter bend meets all dimensional, material, and quality specifications.
Features of Miter Bend :
- Customizable Angles : Miter bends can be fabricated at various angles (e.g., 45°, 90°) to suit specific piping system requirements.
- High-Pressure and Temperature Resistance : Designed to withstand high pressure and temperature conditions, making them suitable for demanding industrial applications.
- Strong and Durable : The welded construction provides high strength and durability, ensuring long service life in harsh environments.
- Smooth Flow Transition : Properly fabricated miter bends offer a smooth flow transition, minimizing pressure drop and turbulence within the piping system.
- Cost-Effective : Miter bends are often more cost-effective than other types of bends, especially for large diameter pipes.
- Versatility : Suitable for a wide range of applications across various industries, including oil and gas, petrochemical, power generation, and water treatment.
- Corrosion Resistance : Depending on the material used, miter bends can offer excellent resistance to corrosion, enhancing their longevity in corrosive environments.
- Ease of Fabrication : Miter bends can be fabricated relatively easily using standard welding and cutting techniques, allowing for quick production and installation.
Miter bends are essential components in piping systems, offering customizable angles, high strength, and durability. Their manufacturing process involves precise cutting, welding, and inspection to ensure high-quality performance. These bends are versatile and cost-effective, making them suitable for a wide range of industrial applications.
Application Of Miter Bend
Oil and Gas Industry | Used in pipelines to change direction and navigate around obstacles while maintaining flow efficiency. Essential for connecting various sections of piping in upstream, midstream, and downstream operations. |
Chemical Processing | Employed in chemical plants to route piping systems around equipment and process units. Facilitates the safe and efficient transport of chemicals and corrosive fluids through complex piping layouts. |
Power Generation | Applied in power plants for redirecting steam, water, and fuel lines. Helps in optimizing the layout of piping systems for boilers, turbines, and cooling systems. |
Water Treatment | Used in water treatment facilities to direct water flow and navigate around treatment equipment. Ensures efficient and effective distribution of treated and raw water throughout the facility. |
Petrochemical Industry | Used in petrochemical plants to manage the direction of hydrocarbon and chemical pipelines. Facilitates the routing of various fluid streams to different processing units and storage tanks. |
HVAC Systems | Employed in heating, ventilation, and air conditioning systems to direct airflow and manage system layouts. Helps in routing ductwork around obstacles and into various sections of a building. |
Marine and Offshore | Utilized in marine and offshore environments to navigate piping systems around equipment and structural supports. Ensures the proper routing of fluids and gases in ships, offshore platforms, and drilling rigs. |
Food and Beverage Processing | Used in food and beverage processing plants to direct sanitary piping systems around equipment. Ensures efficient and hygienic transport of ingredients and finished products. |
Pharmaceutical Industry | Applied in pharmaceutical manufacturing to route sterile piping systems within production facilities. Facilitates the safe and efficient transport of pharmaceutical fluids and ingredients. |
Mining Industry | Used in mining operations for directing slurry, water, and chemical pipelines. Helps in routing pipes through complex and challenging environments in mining sites. |
Fire Protection Systems | Employed in fire protection systems to redirect water or fire suppressant lines around structures. Ensures effective coverage and response capabilities in fire suppression systems. |
Miter Bend Available Types
Stainless Steel 304 Mitered Bend | ASTM A403 WP304 Mitered Bend | Stainless Steel 304L Mitered Bend | ASTM A403 WP304L Mitered Bend |
Stainless Steel 304H Mitered Bend | ASTM A403 WP304H Mitered Bend | Stainless Steel 310 Mitered Bend | ASTM A403 WP310 Mitered Bend |
Stainless Steel 310S Mitered Bend | ASTM A403 WP310S Mitered Bend | Stainless Steel 310H Mitered Bend | ASTM A403 WP310H Mitered Bend |
Stainless Steel 316 Mitered Bend | ASTM A403 WP316 Mitered Bend | Stainless Steel 316L Mitered Bend | ASTM A403 WP316L Mitered Bend |
Stainless Steel 316H Mitered Bend | ASTM A403 WP316H Mitered Bend | Stainless Steel 316Ti Mitered Bend | ASTM A403 WP316Ti Mitered Bend |
Stainless Steel 317 Mitered Bend | ASTM A403 WP317 Mitered Bend | Stainless Steel 317L Mitered Bend | ASTM A403 WP317L Mitered Bend |
Stainless Steel 321 Mitered Bend | ASTM A403 WP321 Mitered Bend | Stainless Steel 321H Mitered Bend | ASTM A403 WP321H Mitered Bend |
Stainless Steel 347 Mitered Bend | ASTM A403 WP347 Mitered Bend | Stainless Steel 446 Mitered Bend | ASTM A403 WP446 Mitered Bend |
Stainless Steel 410 Mitered Bend | ASTM A403 WP410 Mitered Bend | Stainless Steel 904L Mitered Bend | ASTM A403 WP904L Mitered Bend |
Frequently Asked Questions
Most frequent questions and answers