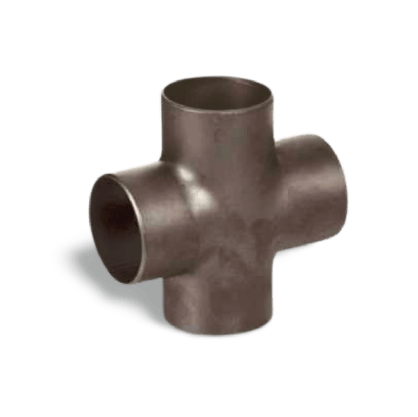
Butt Weld Cross
Teshi Fittings’ Butt Weld Crosses, meticulously designed for diverse industries like Petroleum, Chemical, Hydraulic, and Food sectors. Crafted with precision and adhering to strict international standards, our crosses ensure dependable sealing and seamless integration within piping systems. At Teshi Fittings, we prioritize customer satisfaction, offering unmatched performance and longevity in every fitting. Trust in our expertise and rely on our experience for tailored solutions to meet your project requirements. Elevate your piping systems with Teshi Fittings’ Butt Weld Crosses, setting a new standard of reliability and performance across industries.
Standard Specification of Butt Weld Cross
Dimensions | ASME/ANSI B16.9, ASME B16.28, MSS-SP-43 |
Size | 1/2″NB TO 48″NB IN |
Type | Seamless / ERW / Welded / Fabricated |
DIN | DIN2605, DIN2615, DIN2616, DIN2617, DIN28011 |
EN | EN10253-1, EN10253-2 |
Schedule | Schedule 5S, 10S, 20S, S10, S20, S30, STD, 40S, S40, S60, XS, 80S, S80, S100, S120, S140, S160, XXS and etc. |
Form | Unequal Cross, Equal Cross, Reducing Cross, Pipe Cross, Butt weld Unequal Cross. |
Material & Grades of Butt Weld Cross
Stainless Steel Buttweld Cross | ASTM A403 WP316/316L, ASTM A403 SA / A 774 WP-S, WP-W, WP-WX 304/304L, ASTM A182 F316L, 304L, DIN 1.4301, DIN1.4306, DIN 1.4401, DIN 1.4404 |
Carbon Steel Buttweld Cross | ASTM A234, ASME SA234 WPB , WPBW, WPHY 42, WPHY 46, WPHY 52, WPH 60, WPHY 65 & WPHY 70. |
Low Temperature Buttweld Cross | ASTM A420 WPL3, A420 WPL6 |
Alloy Steel Buttweld Cross | ASTM / ASME A/SA 234 Gr. WP 1, WP 5, WP 9, WP 11, WP 12, WP 22, WP 91 |
Duplex & Super Duplex Steel Buttweld Cross | ASTM A 815, ASME SA 815 UNS NO S31803, S32205. UNS S32750, S32950. Werkstoff No. 1.4462 |
Nickel Alloy Buttweld Cross | ASTM B336, ASME SB336, Nickel 200 (UNS No. No2200), Nickel 201 (UNS No. N02201), Monel 400 (UNS No. N04400), Monel 500 (UNS No. N05500), Inconel 800 (UNS No. N08800), Inconel 825 (UNS No. N08825), Inconel 600 (UNS No. N06600), Inconel 625 (UNS No. N06625), Inconel 601 (UNS No. N06601), Hastelloy C 276 (UNS No. N10276), Alloy 20 (UNS No. N08020), Titanium (Grade I & II), Cupro-Nickel 70/30, CuNi10Fe1Mn, CuNi30Mn1Fe. |
Dimension of Butt Weld Cross
Nominal Pipe Size (NPS) | DN | Outside Diameter at Bevel | Center- to-End | |
---|---|---|---|---|
Run.C | Outlet. M[Notes(1) and (2)] | |||
5 | 125 | 141.3 | 124 | 124 |
6 | 150 | 168.3 | 143 | 143 |
8 | 200 | 219.1 | 178 | 178 |
10 | 250 | 273.0 | 216 | 216 |
12 | 300 | 323.8 | 254 | 254 |
14 | 350 | 355.6 | 279 | 279 |
16 | 400 | 406.4 | 305 | 305 |
18 | 450 | 457 | 343 | 343 |
20 | 500 | 508 | 381 | 381 |
22 | 550 | 559 | 419 | 419 |
24 | 600 | 610 | 432 | 432 |
26 | 650 | 660 | 495 | 495 |
28 | 700 | 711 | 521 | 521 |
30 | 750 | 762 | 559 | 559 |
32 | 800 | 813 | 597 | 597 |
34 | 850 | 864 | 635 | 635 |
36 | 900 | 914 | 673 | 673 |
38 | 950 | 965 | 711 | 711 |
40 | 1000 | 1016 | 749 | 749 |
42 | 1050 | 1067 | 762 | 711 |
44 | 1100 | 1118 | 813 | 762 |
1/2 | 15 | 21.3 | 25 | 25 |
3/4 | 20 | 26.7 | 29 | 29 |
1 | 25 | 33.4 | 38 | 38 |
1-1/4 | 32 | 42.2 | 48 | 48 |
1-1/2 | 40 | 48.3 | 57 | 57 |
2 | 50 | 60.3 | 64 | 64 |
2-1/2 | 65 | 73.0 | 76 | 76 |
3 | 80 | 88.9 | 86 | 86 |
3-1/2 | 90 | 101.6 | 95 | 95 |
4 | 100 | 114.3 | 105 | 105 |
46 | 1150 | 1168 | 851 | 800 |
48 | 1200 | 1219 | 889 | 838 |
Manufacturing process and features of Butt Weld Cross
The manufacturing process of butt weld crosses is quite similar to that of butt weld elbows and reducing tees. Here’s an overview along with the features.
Manufacturing Process:
- Material Selection: Choose suitable materials like carbon steel, stainless steel, or alloy steel.
- Forming: Shape raw materials into the desired cross shape via hot or cold forming methods.
- Cutting and Shaping: Cut and shape the cross blanks to required dimensions, including outlets.
- Welding Preparation: Clean and bevel surfaces of the cross and pipe ends for proper fusion.
- Welding: Assemble and weld using butt welding, heating ends, applying pressure, and allowing fusion.
- Inspection and Testing: Perform thorough inspection, including visual checks, non-destructive testing, and pressure testing.
- Finishing: Apply surface treatments like grinding or polishing for appearance and integrity.
Features:
- Versatility: Facilitates branching off into multiple directions in piping systems.
- Durability: Constructed from high-quality materials for strength and corrosion resistance.
- Leak-Free Joints: Butt welding creates strong, leak-free joints ensuring system integrity.
- Smooth Flow: Smooth interior surface minimizes flow resistance and pressure drop.
- Variety of Sizes: Available in various size configurations for flexibility in design.
- Compliance with Standards: Manufactured to industry standards for quality and compatibility.
Butt weld crosses provide versatility, durability, and reliability for various industrial piping applications.
Application Of Butt Weld Cross
Pipeline Networks | Facilitate branching and fluid distribution in oil and gas, water, and chemical pipelines. |
Process Industries | Direct flow between stages in chemical plants, refineries, and manufacturing facilities. |
Fluid Distribution Systems | Manage fluid flow in HVAC, water treatment, and fire protection systems. |
Power Generation | Route steam, water, or other fluids to turbines, boilers, and heat exchangers in power plants. |
Marine and Offshore Applications | Configure piping systems on ships, offshore platforms, and marine vessels. |
Environmental Engineering | Direct wastewater, slurry, or brine in wastewater treatment and desalination plants. |
Food Processing and Hygiene | Maintain hygiene standards in food processing plants, preventing cross-contamination. |
Mining and Minerals Processing | Direct flow of slurry, chemicals, and water in mining and minerals processing operations. |
Infrastructure Development | Manage utilities flow in construction projects for buildings, pipelines, and transportation. |
Safety and Reliability | Chosen for durability, reliability, and ability to withstand high pressures and temperatures. |
Others Products
Frequently Asked Questions
Most frequent questions and answers